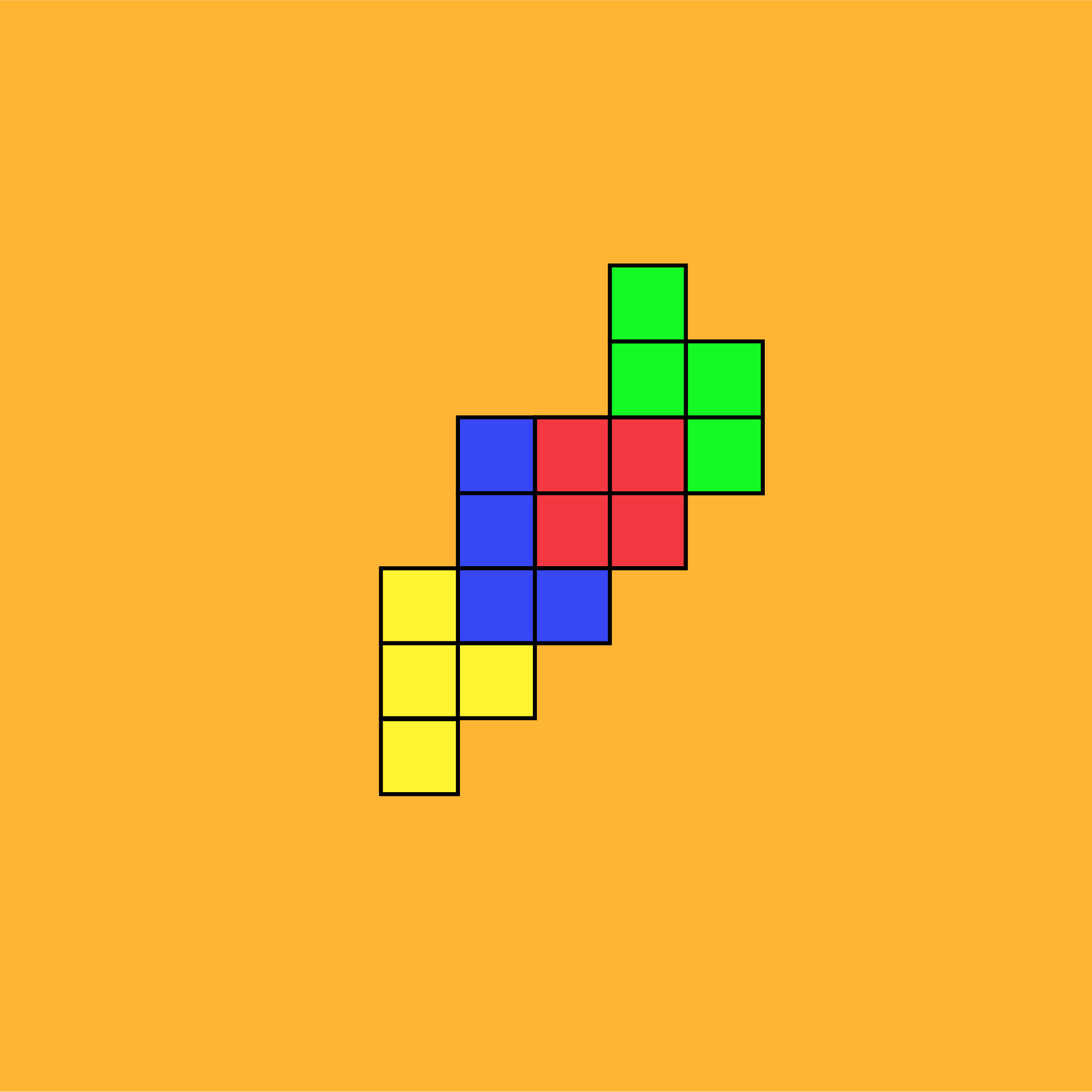
Industrial Layout Project
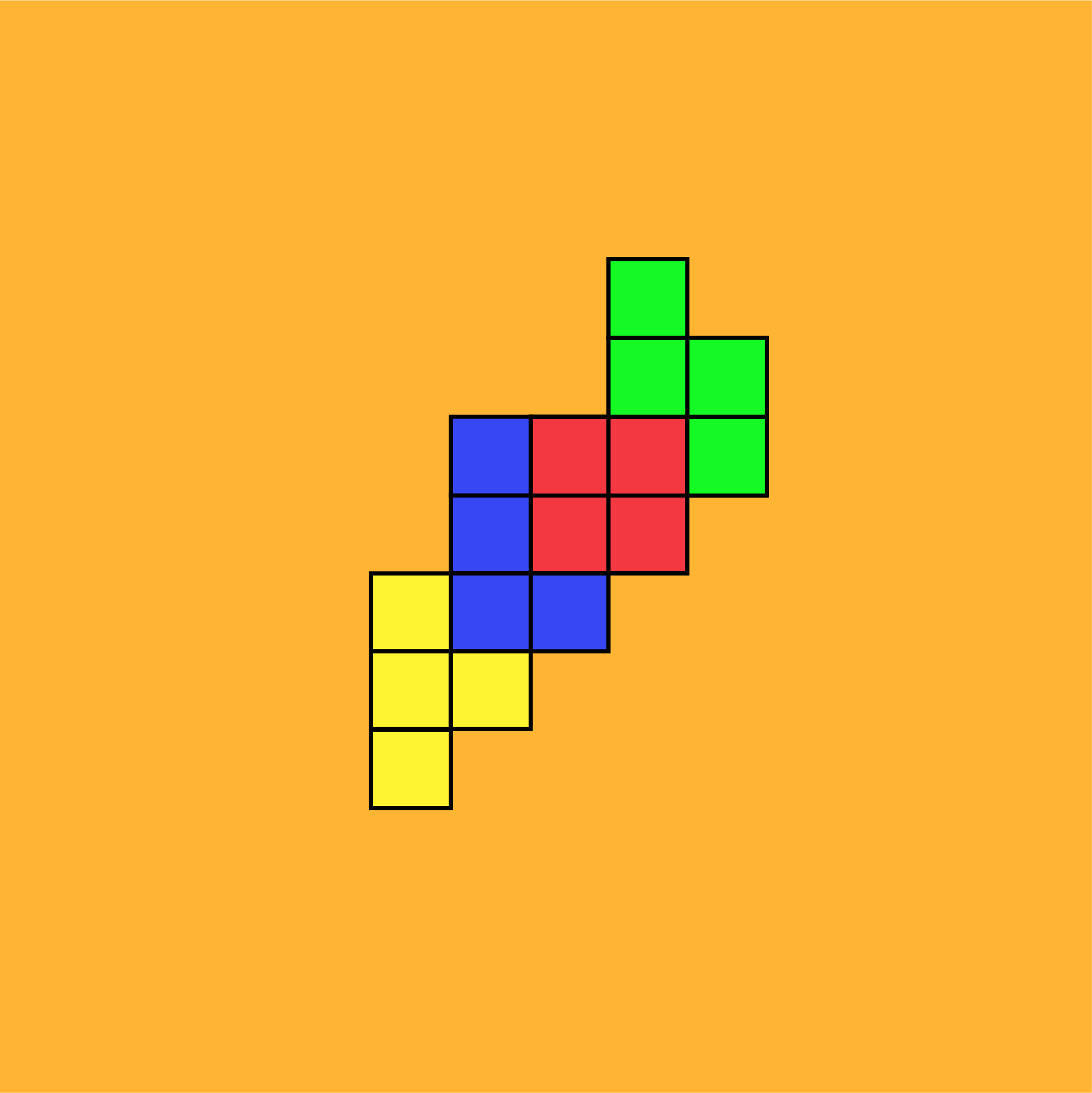
Industrial Layout Project
My role on this project can be imagined as the player of a game of Tetris where I was responsible for seamlessly fitting blocks together.
I managed a team to first determine all of the variations and quantities of pieces that were involved. Each color block represents a production shop producing a major component of an airplanes’ interior. Within each block variation, there were large scale pieces of capital equipment; overhead cranes, moving lines, product curing ovens, office furniture, and various other production related equipment. No two blocks were the same (~39 blocks) with different work flows, scope, constraints, and design requirements to consider.

Concept and Initiation
Through an initial gap analysis, our industrial engineering team determined that the current state business layout would not support future rate increases. The blocks most impacted by this rate increase were scattered throughout the building with no extra space for growth. This space constraint issue led to more discussion on other opportunities that would increase efficiency of flow production for every product stream in our factory. My team was tasked to work with cross-functional leaders to help conceptualize a proposal for all block variations involved.
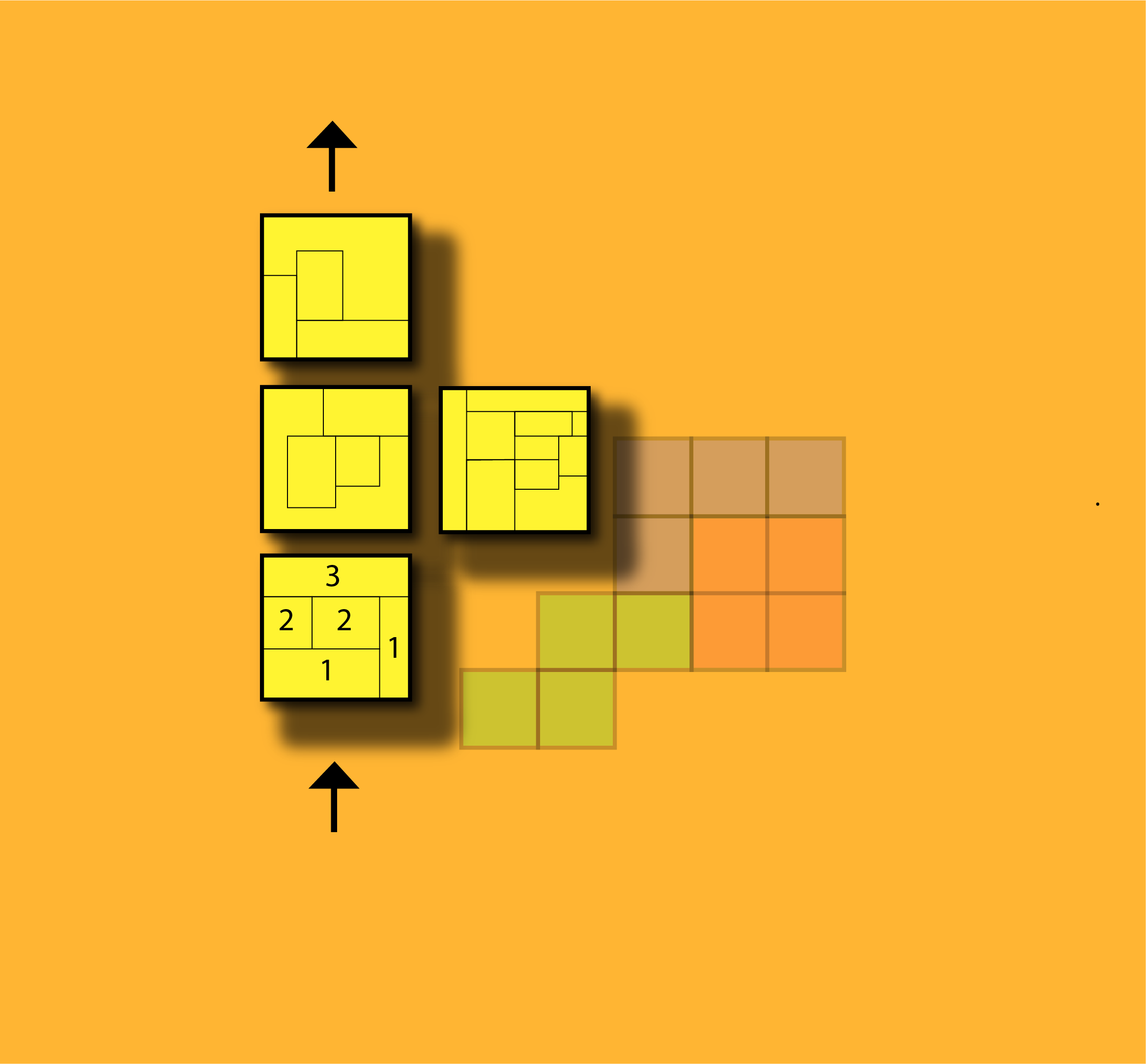
Planning
After the concept proposal was approved for funding, I was tasked to work with users within each block variation to document work processes; flow, interfacing, design requirements, etc. I then worked with various functions (mechanics, engineers, fire and safety teams, construction) to call out utility requirements for equipment. Final layouts submitted to our contract construction teams.

Execution and Monitoring
Problem 1: The team relied on dimensions and item quantities that were provided by users within each block. Certain dimensions and smaller item quantity data were discrepant, which led to scaling issues during the move.
Resolution: Assumed a percentage of risk with space utilization in the next iteration of our planning. Decision captured through change control process and reflected on layouts.
Problem 2: High influx of scope changes reflecting a fluid operations environment.
Resolution: Design revisions had to be iterative with agile management in order to capture the dynamic and complex work flows as they were developing over the course of this project.

Close
Each area had final user interviews and generative feedback via surveys and other data collection methods. Users identified issues and concerns they had with their new layout. We then prioritized items according to their impact on production. Items with low impact or not production critical were deemed out of scope. When all prioritized items were resolved, project was considered closed.
Production Critical Item: Office does not meet safety standards
Root Cause: Office redesign was not part of initial scope, but was out of safety clearance tolerances in existing state
Resolution: Re-design desk arrangement to support proper clearances and egress